生産管理
見積もり・受注からの流れ
Step1見積もり・受注
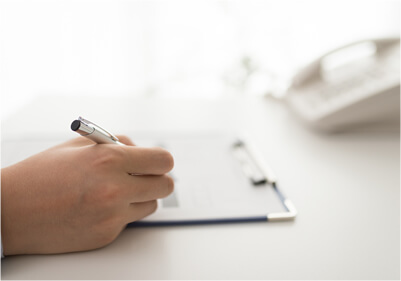
お問い合わせいただいた案件に関して、そもそも製造が可能か、製造するとしたらどのような方法が適しているかを社内にて検討し、
工程・単価・納期をご連絡いたします。
Step2製造
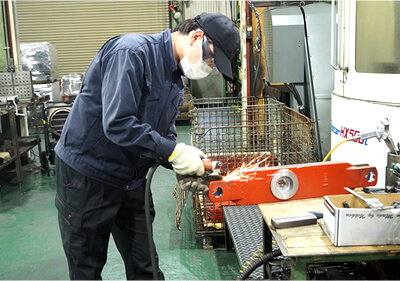
素材が入るまでに、工程手順・加工工具の確認を行い、速やかに加工ができる準備を行います。
旋盤・マシニング・5軸加工機・研磨仕上げまで社内対応している為、スムーズに製品を流すことが出来ます。
更に、CAD/CAMを使用することで複雑な加工も可能にし、段取り時間の短縮にも繋がり、低コスト・最短納期への対応を進めています。
Step3品質管理
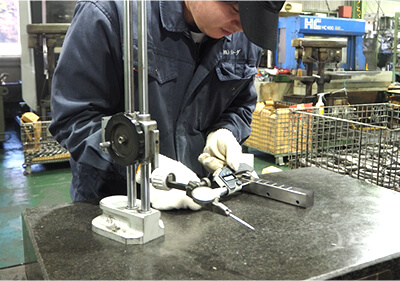
切削加工が終了した製品は、必ず検査を行います。弊社の検査には、各加工工程ごとに
- 初品検査
- 第三者によるダブルチェック
- 抜き取り検査(量産品のみ)
- 終品検査
があり工程の中で不良品を出さない対策を行っています。
また完成品検査においては、温度管理された小型三次元測定器での対応も可能です。
Step4後処理
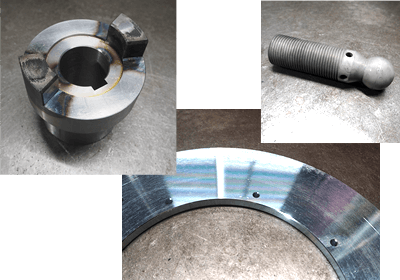
製品の中には、熱処理・メッキ等の後処理が必要なものも多くあります。
これらの処理に関しては信頼の置ける専門の協力会社様へ依頼しております。
Step5梱包・出荷
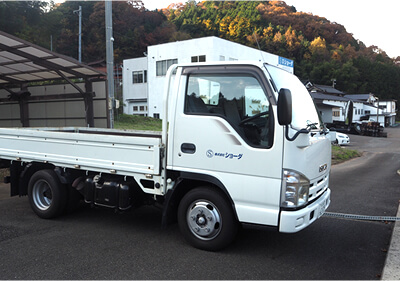
錆びる可能性があるものには防錆処理を行い、
傷つきやすい製品は1点1点個別の梱包をし、出荷もしくは弊社トラックにてお届けいたします。
大型ディスプレイを使用した情報共有
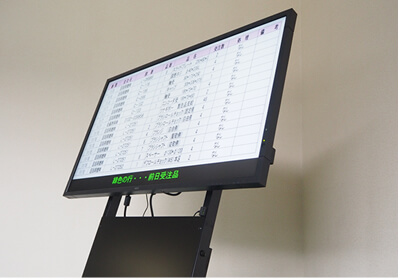
大型ディスプレイを導入し、社内における情報共有を図っています
弊社では、単品から量産品まで1カ月に約200種類の製品が流れるため、納期・顧客名・図番・品名・数量・後処理の有無・材料の納入日をディスプレイに反映し、社内における情報共有を行っています。
映し出す情報は日々更新を行い、リアルタイムな受注状況を共有することで、変更があった際の共有漏れや納期の確認漏れなどを事前に防いでいます。
社内ネットワークによる機械制御・状況管理
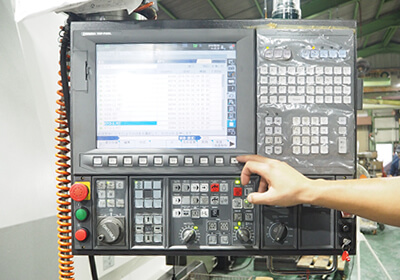
ネットワークシステムを導入し、IoT(Internet of Things)を活用した加工を行っています
事務所に設置しているパソコンと工作機械を社内ネットワークで繋ぎ、加工データ・生産実績・稼働実績・稼働率などのデータをグラフ化し、情報の見える化を行っています。
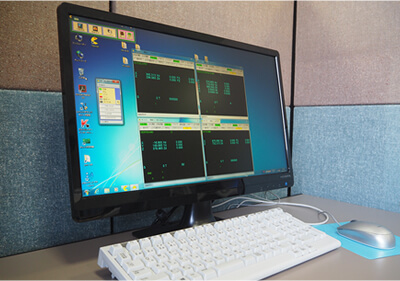
プログラム一元・一括管理を徹底しています
事務所のパソコンでのプログラム一元・一括管理を行い、工作機械操作画面からパソコン内にあるプログラムを引用し使用する事で、加工者のレベルによる加工タイムのバラつきを無くす取り組みを行っています。